The Role of HR in Bridging the Skills Gap in the Manufacturing Industry
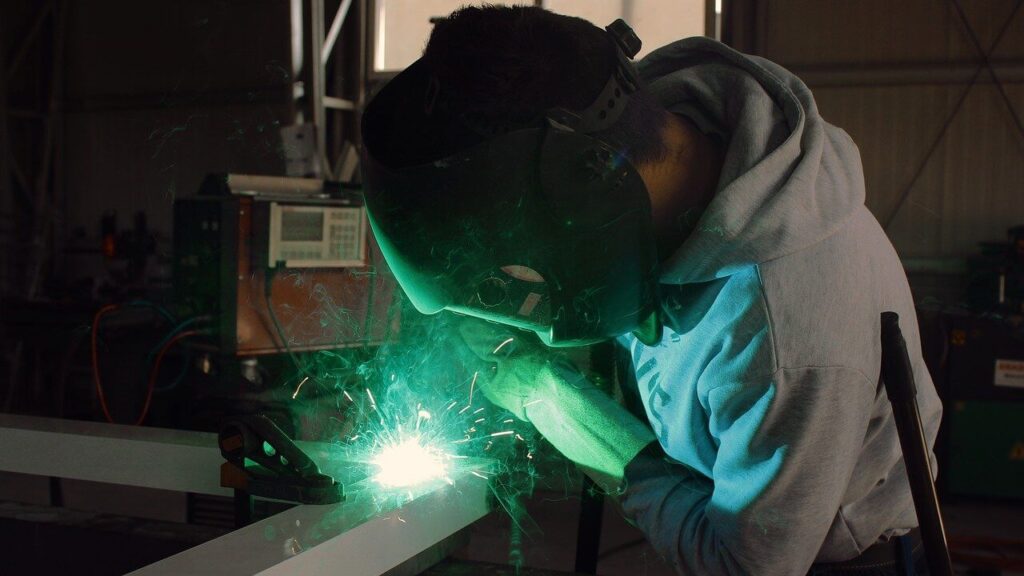
Mundane and repetitive work has become one that needs analytical and problem-solving skills. New technologies such as the Industrial Internet of Things are being used to optimise resources, analyse cross-facility operations, ensure predictive and proactive maintenance of assets, monitor manufacturing operations in real-time, and in areas like supply-chain visibility and safety. This way, plant managers […]